Application of Time Servo System in High Output Steel Project
1. Introduction In China's steel market, the profit margin of medium (thick) plates is relatively large, so the medium (thick) plate production lines of major steel plants have the reputation of “printing machinesâ€. However, with the increasingly fierce market competition and the increasing demand of users for the quality of medium (thick) plates, the major steel plants in China have also increased their investment in the transformation of medium (thick) plate production lines. At present, the slab production method used by the vast majority of manufacturers is: after the slab is heated by three consecutive steel heating furnaces, the hot slab is pushed out from the furnace by a pusher located behind the furnace. By its own weight along the ramp between the outlet of the furnace and the transfer roller path slides over the roller table to complete the tapping process. Such a tapping process not only scratches the lower surface of the slab, affects the surface quality of the slab, but also causes great impact and noise to the transfer roller path and the buffer, which seriously affects the service life of the equipment. How to smooth out the steel over the years has become a problem in the domestic (thick) board production line.
2. Introduction of high-level tapping machine For the problems existing in the current tapping machine, Time Technology and a system integrator in the industry jointly developed a high-level tapping machine. The high-level tapping machine is mainly used in the middle (thick) plate processing field of the steel industry, which solves the problem of the lower surface slippage of the medium (thick) plate in the production process and improves the product quality of the final (middle) plate product. Since this set of tapping machines is still used for the first time in the country, there is no competitor in the country and the added value of the whole set of equipment is high and the profit is large. The whole set of equipment is technologically advanced: Closed-loop hydraulic lifting device and servo control to achieve accurate positioning of all stations are among the leading technologies in China. The whole set of equipment has a wide range of applications and can be applied to all medium (thick) board production lines in China.
(1) High mechanical structure The tapping machine consists of a main girder, a cart, a trolley, a gantry, and an L-shaped hook for taking blanks (see Figure 1). The L-shaped hook has three degrees of freedom: the lateral movement used to complete the selection of the channel is performed by the cart, and the drive form is a motor-reducer-shaft-gear-rack structure; the longitudinal movement used to complete the billet is performed by the trolley. After completion, the drive form is the same as that of the cart; the vertical movement is completed by a gantry in the U-shaped slot of the front pillar of the cart, and is driven by a hydraulic cylinder.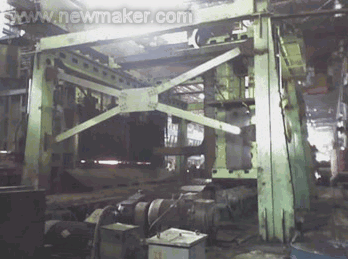
(2) Working process The pusher pushes the slab to the tapping position of the furnace door. This position is completed by laser measurement. Then the furnace door is opened. The trolley drives the tapping machine to advance to the L-shaped hook. The slab is located in the furnace. After stopping at the lower position, the L-shaped hook lifts up and lifts the slab away from the furnace rail. The trolley drives the steel machine back to the top of the conveyor roller conveyor. The furnace door closes and the L-shaped hook steadily decreases, smoothing the slab. Placed on the transfer roller, the roller rotates to transport the slab, and the L-shaped hook is again raised to its original position. At this point, the tapping machine completes a tapping cycle. The carts are traversed as required, so that the L-shaped hooks are aligned with the left, middle, or right tapping positions of the furnace. To facilitate the realization and completion of the next tapping cycle.
(3) Electrical control system The high-level tapping machine electrical control system consists of a Siemens programmable controller, a time IMS servo controller, and the like. The system configuration scheme is shown in Figure 2.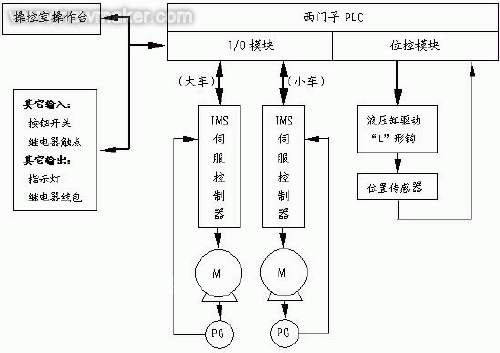
a. The motor can work stably in the working range of 0.01Hz~250Hz. b. The motor's rated torque output can be 3 times when the motor's operating speed is lower than 60Hz, including 3 times the rated torque output of the motor when 0Hz is locked (effectively solved Frequency conversion starting torque compensation and brake input when starting and stopping the motor).
c. Utilize the built-in PLC function (16 input/13 output) of Time IMS servo controller to use I/O method to inform the host PLC whether the controlled motor has completed the accurate positioning action. The upper PLC verifies the actual mechanical positioning result through the corresponding proximity switch signal. does it reach the requirement. The IMS servo controller realizes the accurate positioning of the controlled motor and meets the system requirements in one positioning. It effectively avoids repeated positioning and repeated actions. Not only improve the system's work efficiency, enhance the system's anti-jamming performance, but also greatly simplifies the upper computer's computing work.
d. Programs compiled using the QMCL language can not only be electrically compensated by various types of gaps, but also can be arbitrarily set by the user parameters. Effectively avoid the positioning error caused by the change of mechanical clearance after the equipment is put into use for a long time.
e. System parameters arbitrarily set the S curve and torque limit value of the motor during operation.
f, with 2 programmable D / A output, can achieve any monitoring item analog output.
g. After using the time IMS servo controller to control the carts and trolley motors, the upper computer Siemens PLC can realize the positioning control and detection of carts and trolleys only through electrical contact input/output (that is, the system adopts a semi-closed loop control method. ), Reducing the related wiring, effectively avoiding the introduction of more vulnerable links for the entire system, and enhancing the stability and reliability of the entire system.
h. Because the front end of the car has a high ambient temperature, it is not convenient to install proximity switches and other electrical components. However, the system requires that the water-cooled device be turned on after the car advances to a certain position, and the target position arrival signal is given after reaching the target position. Therefore, it is necessary for the controller to know its location during the action of the trolley and to provide corresponding input/output signals. The IMS servo controller is equipped with an integrated PLC function (16-point input/13-point output). This is combined with the encoder feedback pulse data. The above functions can be realized by executing the program compiled by the QMCL language software.
i. IMS servo controller's unique 0Hz lock function can realize the "electric brake" action of the motor. This not only ensures the final positioning accuracy after the positioning control is completed, but also eliminates the wear of the motor holding brake pad and the positional offset generated during the mechanical holding brake process. In order to ensure that the system will not bring security risks in case of power loss, the system does not remove the mechanical brake of the relevant motor, but the function of the motor mechanical brake is limited to power-off protection.
j. Due to the use of flexible QMCL software programming, IMS servo controllers can be adapted to meet the needs of the customer at any time during the commissioning process whenever the final customer request changes or increases or decreases.
3, the effect of the operation (1) traversing rate of cart operation: 1.574 ~ 314.8mm / s
Middle to left practical work route: 2300mm
Middle Road to the right road actual work schedule: 2300mm
Positioning accuracy: 0.002373mm
(2) Advancing and retreating speed of the trolley: 1.574 to 314.8mm/s
Actual work schedule: 2998.74mm
Positioning accuracy: 0.002373mm
2. Introduction of high-level tapping machine For the problems existing in the current tapping machine, Time Technology and a system integrator in the industry jointly developed a high-level tapping machine. The high-level tapping machine is mainly used in the middle (thick) plate processing field of the steel industry, which solves the problem of the lower surface slippage of the medium (thick) plate in the production process and improves the product quality of the final (middle) plate product. Since this set of tapping machines is still used for the first time in the country, there is no competitor in the country and the added value of the whole set of equipment is high and the profit is large. The whole set of equipment is technologically advanced: Closed-loop hydraulic lifting device and servo control to achieve accurate positioning of all stations are among the leading technologies in China. The whole set of equipment has a wide range of applications and can be applied to all medium (thick) board production lines in China.
(1) High mechanical structure The tapping machine consists of a main girder, a cart, a trolley, a gantry, and an L-shaped hook for taking blanks (see Figure 1). The L-shaped hook has three degrees of freedom: the lateral movement used to complete the selection of the channel is performed by the cart, and the drive form is a motor-reducer-shaft-gear-rack structure; the longitudinal movement used to complete the billet is performed by the trolley. After completion, the drive form is the same as that of the cart; the vertical movement is completed by a gantry in the U-shaped slot of the front pillar of the cart, and is driven by a hydraulic cylinder.
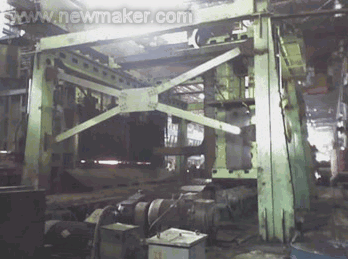
Figure 1 high position tapping machine
(2) Working process The pusher pushes the slab to the tapping position of the furnace door. This position is completed by laser measurement. Then the furnace door is opened. The trolley drives the tapping machine to advance to the L-shaped hook. The slab is located in the furnace. After stopping at the lower position, the L-shaped hook lifts up and lifts the slab away from the furnace rail. The trolley drives the steel machine back to the top of the conveyor roller conveyor. The furnace door closes and the L-shaped hook steadily decreases, smoothing the slab. Placed on the transfer roller, the roller rotates to transport the slab, and the L-shaped hook is again raised to its original position. At this point, the tapping machine completes a tapping cycle. The carts are traversed as required, so that the L-shaped hooks are aligned with the left, middle, or right tapping positions of the furnace. To facilitate the realization and completion of the next tapping cycle.
(3) Electrical control system The high-level tapping machine electrical control system consists of a Siemens programmable controller, a time IMS servo controller, and the like. The system configuration scheme is shown in Figure 2.
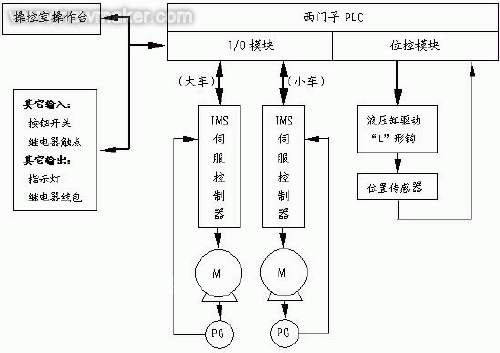
Figure 2 system composition
a. The motor can work stably in the working range of 0.01Hz~250Hz. b. The motor's rated torque output can be 3 times when the motor's operating speed is lower than 60Hz, including 3 times the rated torque output of the motor when 0Hz is locked (effectively solved Frequency conversion starting torque compensation and brake input when starting and stopping the motor).
c. Utilize the built-in PLC function (16 input/13 output) of Time IMS servo controller to use I/O method to inform the host PLC whether the controlled motor has completed the accurate positioning action. The upper PLC verifies the actual mechanical positioning result through the corresponding proximity switch signal. does it reach the requirement. The IMS servo controller realizes the accurate positioning of the controlled motor and meets the system requirements in one positioning. It effectively avoids repeated positioning and repeated actions. Not only improve the system's work efficiency, enhance the system's anti-jamming performance, but also greatly simplifies the upper computer's computing work.
d. Programs compiled using the QMCL language can not only be electrically compensated by various types of gaps, but also can be arbitrarily set by the user parameters. Effectively avoid the positioning error caused by the change of mechanical clearance after the equipment is put into use for a long time.
e. System parameters arbitrarily set the S curve and torque limit value of the motor during operation.
f, with 2 programmable D / A output, can achieve any monitoring item analog output.
g. After using the time IMS servo controller to control the carts and trolley motors, the upper computer Siemens PLC can realize the positioning control and detection of carts and trolleys only through electrical contact input/output (that is, the system adopts a semi-closed loop control method. ), Reducing the related wiring, effectively avoiding the introduction of more vulnerable links for the entire system, and enhancing the stability and reliability of the entire system.
h. Because the front end of the car has a high ambient temperature, it is not convenient to install proximity switches and other electrical components. However, the system requires that the water-cooled device be turned on after the car advances to a certain position, and the target position arrival signal is given after reaching the target position. Therefore, it is necessary for the controller to know its location during the action of the trolley and to provide corresponding input/output signals. The IMS servo controller is equipped with an integrated PLC function (16-point input/13-point output). This is combined with the encoder feedback pulse data. The above functions can be realized by executing the program compiled by the QMCL language software.
i. IMS servo controller's unique 0Hz lock function can realize the "electric brake" action of the motor. This not only ensures the final positioning accuracy after the positioning control is completed, but also eliminates the wear of the motor holding brake pad and the positional offset generated during the mechanical holding brake process. In order to ensure that the system will not bring security risks in case of power loss, the system does not remove the mechanical brake of the relevant motor, but the function of the motor mechanical brake is limited to power-off protection.
j. Due to the use of flexible QMCL software programming, IMS servo controllers can be adapted to meet the needs of the customer at any time during the commissioning process whenever the final customer request changes or increases or decreases.
3, the effect of the operation (1) traversing rate of cart operation: 1.574 ~ 314.8mm / s
Middle to left practical work route: 2300mm
Middle Road to the right road actual work schedule: 2300mm
Positioning accuracy: 0.002373mm
(2) Advancing and retreating speed of the trolley: 1.574 to 314.8mm/s
Actual work schedule: 2998.74mm
Positioning accuracy: 0.002373mm
Linear Bearing,Linear Bearings Lmf12uu,Linear Bearings Lmf25uu
Autos Ball Bearing Co., Ltd. , http://www.qdrollerbearing.com