Determining the Quality of Fiberglass Molded Water Tanks
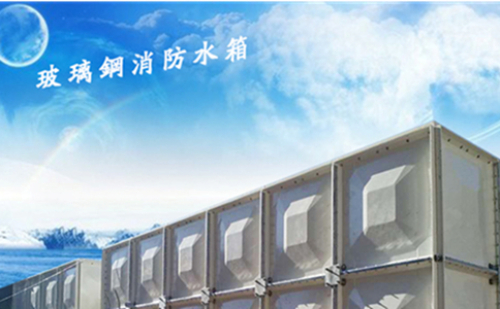
Guided Reading: Molded steel tanks are assembled from the SMC molded plates, seals, metal structures and piping systems. Gives great convenience to design and construction. The general water tank is designed according to the standard, and the special water tank needs to be specially designed. According to user needs can be assembled 0.125-1500 cubic meters of water tanks. If the original water tank needs to be replaced, there is no need to transform the house and the adaptability is very strong. Specially developed styling product sealing tape, the sealing tape is non-toxic, water-resistant, elastic, permanent deformation, tightly sealed. The tank has high overall strength, no leakage, no deformation, and convenient maintenance and inspection. FRP molded water tank is a new type of water tank that is currently used internationally. The overall quality of the SMC tank assembly assembled. Its characteristics are the use of food-grade resin, so the water quality is good, clean and pollution-free; with high strength, light weight, corrosion resistance, good looks, long life, easy maintenance and management.
Determine the three elements of FRP molded tank quality
First, synthetic resin
Synthetic resin is the base material that determines the quality of FRP water tank. Loose glass fiber is bonded together as a whole. It mainly acts as a transfer stress. Therefore, resin plays an important role in the strength of FRP tanks, especially in compression, bending, twisting and shearing. The shear strength is even more pronounced. The resin content also affects the performance of FRP tanks. Usually the resin content is 20%-35%, which is related to the molding method and the type of reinforcing materials. For example, winding and compression molding, the resin content is low, while the hand lay-up, the resin content is slightly higher. The strength layer resin content is slightly lower, usually between 25% -40%; corrosion resistance, anti-seepage layer resin content is higher, generally more than 50% with glass cloth as a reinforcing material, resin content is lower than with glass mat. When the glass fiber surface felt is used as a reinforcing material, the content of the resin can be more than 85%. In addition, the resin is the matrix material that determines the quality of the FRP tank. It affects the elastic modulus, heat resistance, electrical insulation, electromagnetic wave transmission, chemical resistance, weather resistance, and aging resistance of FRP. For example, the chemical liquid etch resistance and water resistance of glass fiber depends mainly on the properties of the resin matrix. Usually unsaturated polyester resin 197# is resistant to chemical corrosion, while 1289# is better water resistant. Different types and grades of resins have different properties.
Second, glass fiber
Glass fiber is the main bearing part that determines the quality of FRP water tank. It can not only improve the strength and elastic modulus of FRP, but also reduce the shrinkage deformation and increase the heat distortion temperature and impact strength at low temperature. For example 306# polyester resin castings after adding 50% glass cloth. The tensile strength can be increased from 50MPa to 200MPa, and the tensile modulus can be increased from 3.9GPa to 14GPa.
Third, the interface
The so-called interface is the interface between any two-phase substances.
The quality of FRP water tanks is not only related to the reinforcing materials and synthetic resins used, but also to a large extent related to the bonding and durability of the interface between fibers and resins.
As we all know, glass fiber is a cylindrical glass, the surface is also as smooth as glass, and the surface is often firmly adsorbed with a thin layer of water, which of course affect the bonding properties of glass fiber and resin. In particular, in the process of drawing textiles, glass fibers are often coated with a sizing agent for purposes such as bundling, lubrication, and elimination of static electricity. Most of these sizing agents are paraffin-based substances that remain on the surface of glass fibers for synthetic resins. Separation from the glass fiber, preventing the two bonding. Visible interface has a great influence on the performance of FRP. Problems with the interface need to be addressed. For example, the glass fiber surface is covered with a surface treatment agent so that the glass fiber and the resin can be firmly bonded together. This method is a very effective way to improve the quality of FRP tanks, both at home and abroad are vigorously researched and adopted. Practice has proved that glass fiber and its fabric, after being treated with a surface treatment agent, not only improve the wear resistance, water resistance, and electrical insulation properties of glass fiber, but also enhance the strength of the quality of the glass fiber reinforced plastic water tank, especially in the wet conditions. . It can be seen that the factors affecting the quality of FRP tanks are not only the two major components of glass fiber and resin, but also the interface is very important. These three major elements are indispensable. They are closely related and inseparable.
Source: Texas Techno Environmental Protection Technology Co., Ltd.
Wood pellet complete production line is euipment for making the wood log/wood chips/sawdust/wood shaving/rice husk/stalk/grass...raw material into fuel pellets, Main process: Wood Chipper --hammer mill--biomass dryer--Biomass Pellet Machine--pellet cooler--Pellet Packing Machine.
Wood chipper: make the wood log/wood branches/wood blocks/bamboo... into smaller chips. Finished products: 20-50cm.
Hammer Mill/Crusher: crush the wood chips/wood shaving/small blocks/grass/stalk...to 6-8mm powder. Finished products: 6-8mm.
Rotary Dryer: dry raw material into suitable moisture to produce high-level pellets. Finished moisture: 10-15%
Wood Pellet Machine: press crushed and dry sawdust/rice husk/straw/grass... into pellets. Finished pellets: 6/8/10mm.(Asian Market standard: 8mm; European Market standard: 6mm)
Cooling Machine: cool high-temperature pellets before packing.
Reason: the finished pellets are very hot and realease moisture as they leave the pellet machine. This section can ensure to generate smooth pellets.
Packing Machine: pack pellets into 20-50kg/bag or 1 ton bag. Advantage: easily to be transported to final users' site.
Pellet Machine Line,Straw Hay Pellet Production Line,Straw Materials Pellet Production Line,Straw Pellet Production Line
Shandong Kingoro Machinery Co., Ltd , https://www.kingoromachinery.com