Four major automotive supplier 48V hybrid battery system design
Bosch 48V Hybrid Products
In 2017, Bosch made significant progress in the field of electrification. The newly developed 48V hybrid battery from Bosch can be quickly integrated into new models, helping existing car manufacturers and similar start-ups to shorten development cycles and save costs.
The lithium-ion battery can be installed in many models, such as compact cars, mini cars and mini cars, and it is expected that the battery will begin mass production by the end of 2018.
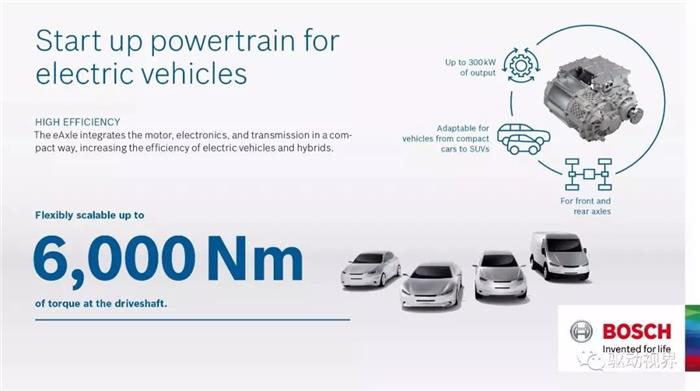

Taking into account the market's huge demand for entry-level hybrid models, Bosch will also provide powertrain components other than 48V batteries. Bosch expects that by the year 2025, about 15 million 48V hybrid vehicles will be on the road.
Bosch Electric Drive Bridge Products
By 2019, Bosch's new eAxle will further increase the mileage of electric vehicles.
It is reported that through an expandable and modular platform, Bosch's electric axis drive system (eAxle) brings motorization to car manufacturers. Compared to independent drive components, the drive system's cost efficiency can be increased by 5%-10%. eAxle can be applied to multiple automotive platforms and combines Bosch's top powertrain components into one system.
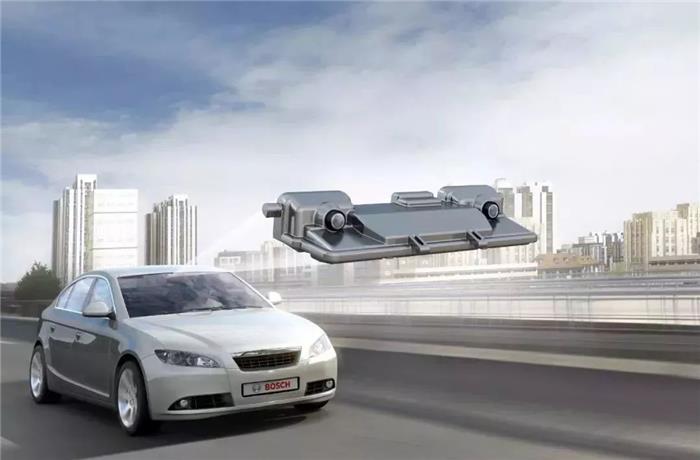

Bosch said that the newly introduced "fully integrated powertrain" is 20% smaller than the conventional electric vehicle powertrain. In addition, the production costs of the new powertrain are also lower. Bosch did not disclose the specifications of the "eAxle" power unit.
Bosch abandons electric vehicle battery business
After careful consideration, Bosch announced that it will abandon its self-produced power battery cells and instead provide customers with a complete battery system through outsourcing of battery cells and its own powerful battery management system technology and system integration capabilities.
In this regard, Rolf Bulander gave four reasons:
Market level: The global power battery market is dominated by the five largest companies in Asia (Ningde times, Japan’s Panasonic, South Korea’s Samsung, South Korea’s LG, and Shenzhen’s BYD), and these have become the climate. If Bosch were to produce battery cells at this time, it would not only account for What is cheap, but also take great market risks.
Technical level: The new technology of power batteries emerges in an endless stream and it is imminent to replace them with new ones. The current energy density of lithium batteries based on liquid electrolytes is still insufficient to meet the demand for electric vehicles. Bosch is more optimistic about solid-state batteries and next-generation lithium battery technologies, but it is expected to mature by 2025.
Cost level: 75% of the cost of a battery cell comes from lithium and other raw materials, plus processing, packaging, transportation and other expenses, the profit space is very limited, once the price war is fought, it can be said that earn less than a few dollars.
Investment level: By 2030, the global power battery capacity will reach 1000GkWh. If Bosch's market share is to reach 20%, then it needs to invest at least 20 billion euros to purchase battery cell production, testing, recycling and other equipment. This money is not a small amount for any part company. What's more, once there is a revolutionary innovation in technology, the upfront investment is likely to be overdone.
However, this does not mean that Bosch has abandoned the development and manufacture of battery systems. Not only that, Bosch also continues to increase its research and development efforts in this field.
Rolf Bulander is confident in the future of power battery technology. He believes that Bosch's advantages in this field are concentrated in three aspects:
With the integration capability of “Sankyo†(battery, motor and electronic control) systems, Bosch is one of the few companies in the world that currently has a full range of R&D capabilities and core technologies for powerful electric drive systems, battery management, and vehicle control. .
The energy efficiency core know-how, Bosch is developing next-generation motors, inverters, and automotive thermal management systems that are more energy-efficient, using Bosch's systems, and with the same amount of power, the vehicle has a longer cruising range.
Standardization, Bosch's goal is to continue to improve electric technology and reduce costs through standardized design and management, making electric drive vehicles truly into the era of large-scale application.
2 ZF ZF
ZF Hybrid Products
In the hybrid electric drive system, ZF can provide full vehicle manufacturers with a full range of hybrid components. Whether it is micro-mixing or full-blown mixing, zf can customize the specific solution for the customer according to the different hybrid degree of the transmission.
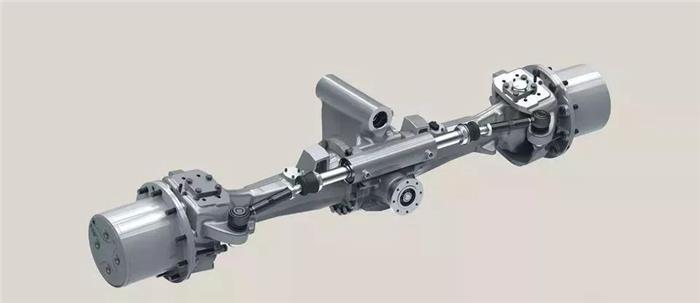

At present, ZF hybrid version of the 8-speed automatic transmission has been used in many production models (such as the BMW Activehybrid 7 models and Audi Q5 hybrid quattro models use this).
According to the manufacturer's introduction to the future, ZF also plans to launch a hybrid version of a 9-speed automatic transmission designed to match the passenger car with the front transverse engine. In the country, ZF actually carries many matching tasks, such as matching engine and gearbox for many car companies.
ZF also is committed to the development of advanced automatic transmissions, such as 8-speed plug-in hybrid transmission systems. It integrates a high-performance motor in the bell jar instead of the torque converter, enabling the vehicle to use pure electric driving to reach a top speed of 120 kilometers per hour, thus achieving zero local emissions.
ZF's hybrid product portfolio includes motors in various performance categories and is equipped with fully compatible control units, software and power electronics components designed and manufactured by ZF.
ZF electric drive axle and integrated electric drive system
In order to achieve pure electric and zero emissions, zf has developed a central electric drive product for small and medium-sized passenger vehicles to accommodate more and more car manufacturers for the positive development model of electric vehicles. This product is located in the middle of the car axle. With a maximum power of 120 kilowatts, even at low speeds, high torque values ​​can be output, and its acceleration performance is no less than that of conventional internal combustion engines.
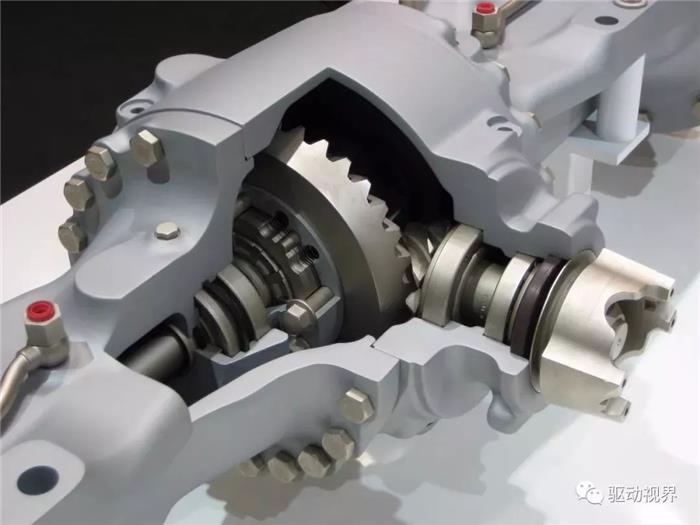

In addition, this central electric drive product has a compact structure, weighs only about 45 kilograms, and is easy to arrange power batteries before and after the vehicle to achieve better controllability and stability. The balanced arrangement of the power battery before and after is considered to be the current mainstream layout. The BMW i3 and teslamodels new electric vehicle chassis design models have adopted this arrangement.
For many pure electric vehicles, the electric motor and the inverter work together to generate a certain amount of energy loss during a specific driving condition. ZF's electric drive unit provides a solution to this problem. ZF Through optimizing the performance of the entire electric drive system, the power conversion efficiency is improved by 6%.
Integrated power supply is a major feature of this device. At the same time, ZF is also developing modular systems for various output levels to better meet the needs of different customers and vehicles. In the future, ZF electric drive systems will no longer apply to small cars and compact cars, but will rely on axle hybrid modules to further expand the product line to mid- to high-class front-wheel drive cars.
ZF chassis, electric drive and transmission
ZF's chassis is available from ball hinges, shock absorbers to complete axle systems. Its advantage in this area is that it can provide solutions for the entire axle system (for example, chassis and suspension can be adjusted according to models). , including the chassis NVH optimization, in the country it provides ABB with the entire axle service) and provides some high-tech products such as ZF's stepless variable damper control shock absorber (CDC for short) according to different driving Working conditions, real-time optimization of the damping force on each wheel.
The ZF Active Rear-wheel Steering System (AKC), which was put into mass production in 2013, assists the steering of the front axle by changing the toe angle of the rear wheels of the rear wheels through an electromechanical actuator, providing vehicle handling and safety. For example, in terms of chassis lightweight technology, ZF’s latest display of leaf springs made of glass fiber plastic (GRP), compared to the traditional steel structure axle, the weight of the lightweight axle developed by ZF can be up to With a 15% reduction, the weight of the lightweight pillared suspension module is only half that of traditional steel-aluminum structural products.
Similarly, ZF offers a fully integrated driveline and chassis solution for conventional vehicles in the form of a modular rear axle concept. With the electric bridge drive and ZF's Active Rear Wheel Steering (AKC), this initiative for steering functions can be easily upgraded.
For example, compared to the current mainstream 6-speed gearbox, ZF's 9-speed automatic transmission (9HP) has a high gear ratio of 9.81, which can reduce fuel consumption by an additional 16%. However, it is noted that this efficiency is 120 km. / When measured at constant speed, so the actual fuel economy is certainly not so obvious.
3 Japan Denso DENSO
Teamed up with Toyota and Mazda
Japanese car companies Toyota, Mazda and large automotive parts manufacturers Denso announced that the three companies signed a contract for cooperation in research and development of electric vehicle-related technologies and decided to establish a new company for this purpose.
The three companies stated in a joint press release issued on the 28th that Toyota, Mazda and Denso will all contribute 10 million yen (1 US dollar totaling 112.7 yen) in a ratio of 90%, 5%, and 5% respectively.
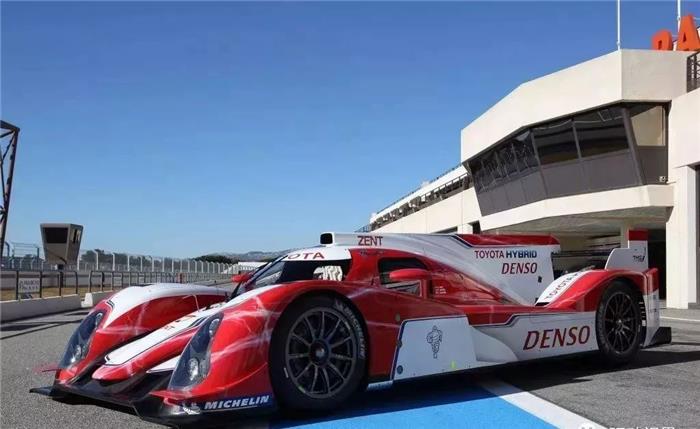

The new company is headquartered in Nagoya City, which is not far from Toyota's headquarters. It is mainly engaged in the research and development of technologies related to the basic structure of electric vehicles covering all levels and models. The new company’s full-time engineers are mainly seconded from three companies.
Set up factory in the United States to produce electronically controlled components
In recent years, many countries and regions around the world have increasingly stricter restrictions on greenhouse gas emissions, and some places have even stipulated that there must be a certain percentage of electric vehicles in sales vehicles.
Nippon Denso will invest US$1 billion to transform its plant in Maryville, Tennessee, USA, to produce electric vehicles, hybrid cars and self-driving auto parts.
As more and more automakers announce their plan to produce electric vehicles in the United States, the huge investment in Japan's Denso will help resolve the problems that have plagued the electric vehicle industry recently.
Nippon Denso will invest in the construction of three production lines in the United States, namely: EV inverters, radar components and data control modules for future connected cars, while others Japan’s auto giants produce these parts in Japan.
This move has solved Toyota’s immediate needs. Toyota is the largest customer of Denso in Japan and a major shareholder of Denso. Toyota plans to build a factory in the United States to produce one or more electric cars with Mazda, but the name of the car is not yet determined.
Senior Denso executives revealed at the Maryville plant last week that they will expand production lines and produce electrified products for hybrid and electric vehicles, which are highly secure and can interconnect networks. In addition, they will provide these parts for customers throughout North America.
Electric cars are no longer the marginal losers. As another important customer of Denso, it was revealed last week that in the next 18 months, GM will introduce two new types of electric vehicles. In addition, as of 2023, the company will add 20 new electric vehicles or hydrogen fuel cell vehicles.
Nippon Denso and Kyoto University jointly develop electronic control products
Denso announced a partnership with FLOSFIA, a technology startup founded by Kyoto University, to invest in and develop next-generation power semiconductor devices that are expected to reduce and reduce power consumption, cost, size and weight for inverters used in electric vehicles. Through joint development projects, the two companies aim to improve the efficiency of electric vehicle power control units, which is the key to promoting the widespread use of electric vehicles.
In addition, Denso acquired new shares issued by FLOSFIA in its Series C financing of 800 million yen (about US$7.1 million). Other investors in the C-Series include Mitsubishi Heavy, Mitsui Kinzoku-SBI Material Innovation Fund, and Even Roads Investment.
FLOSFIA successfully prepared a Schottky barrier diode (SBD) with α-Ga2O3, and its conduction loss was reduced by 86% compared to SBD based on SiC. Denso said that α-Ga2O3 can replace current silicon (Si) and silicon carbide (SiC) power semiconductors and help further develop technologies that support future electric vehicles. The two companies will further develop high-voltage product technologies for hybrid and electric vehicles, including semiconductors.
4 Schaeffler Schaeffler
Schaeffler's hybrid products
Although the Chinese government has spared no effort to promote electric vehicles and regards electric vehicles as the future development direction, some auto OEMs and core component manufacturers have still not given up on this technology route of hybrid power. On March 16th, Schaeffler Group's first P2 hybrid module, the world’s leading supplier of automotive engines, transmissions and chassis components and systems, was put into operation at the Taicang plant in Jiangsu, providing a systematic solution for domestic auto companies to develop hybrid models. .
The P2 hybrid module is Schaeffler's representative product in the field of electric drives. This product can be applied in a modular way to hybrid vehicles with different types of gearboxes. Depending on the location of the hybrid module, there are various configurations such as P0, P1, P2, P3, and P4.
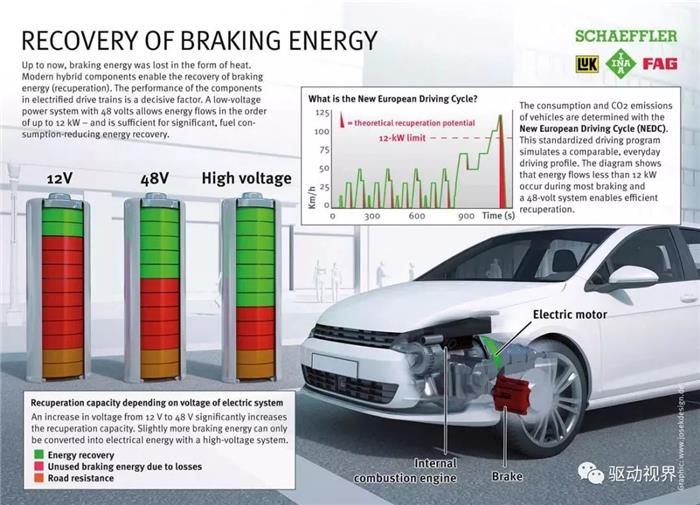

The P2 hybrid module is located between the engine and the transmission. Unlike the PS configuration of Toyota THS and Universal Voltec, the P2 configuration is relatively simple, adapting to different gearboxes and engines, and is particularly suited for dual-clutch gearboxes. Moreover, the cost of the P2 configuration is lower.
The Schaeffler P2 Hybrid Module consists of a high power density permanent magnet synchronous motor, a dry K0 clutch and a central motor actuator. The entire system can integrate motors from 25 kW to 80 kW, delivering up to 250 Nm of torque through the clutch (up to 800 Nm with a one-way clutch).
The module can implement a variety of drive modes, including pure electric drive vehicle starting and running, pure engine driven travel, motor assist, electric motor starting in purely electric driving, and braking energy recovery.
Schaeffler establishes new electric drive division
In the middle of last year, Schaeffler announced that from January 1st, 2018, an independent electric drive business unit will be established under the Automotive Division to integrate all product and system solutions related to hybrid and pure electric applications. The new business unit in Boer, Germany is also the new headquarters of the Schaeffler Group Automotive Division.
In addition, the Schaeffler Group has also established a preliminary sales plan in the field of electrification, and it is expected that the electric vehicle business will account for more than 15% of total revenue by 2020.
On January 16, 2018, Schaeffler formally appointed Dr. Jochen Schröder as the head of the newly established electric drive business unit of Schaeffler Group. He will start from April 1, 2018 Formally took office. In this position, Dr. Schroeder will report to the Chief Executive Officer of the Schaeffler Group's Automotive Division, Mattis Lenk.
Dr. Schroeder, aged 46, worked for Valeo Siemens eAutomotive before joining the Schaeffler Group. As a member of the Management Committee, he is mainly responsible for the company's global R & D business.
Dr Schröder studied at the Hamburg-Harburg Institute of Technology and received a doctorate in control engineering. He once worked for BMW and worked in different management positions. He was responsible for system design, electric drive advanced engineering development and vehicle energy management.
At the end of 2016, after serving for 15 years at BMW, Dr. Schroeder joined Valeo Siemens eAutomotive as a CTO.
Schaeffler Electric Drive Bridge
A few days ago, Schaeffler Group released a new strategic goal slogan "Tomorrow's Plan". Group CEO Klaus Rosenfeld said: "The automotive industry is undergoing rapid transformation. If we want to catch up with changes in the market, we need to speed up. As a result of its own transformation, the Schaeffler Group will transform its pure electric vehicle solutions, Industry 4.0 and smart car digital technologies, which will account for 15% of the group's sales in 2020."
It is understood that the Schaeffler Group has received eight series of contracts for different automotive customers around the world for new energy vehicle driveshafts and hybrid modules. The sales potential of these contracts exceeds 1 billion euros. It is worth mentioning that Schaeffler Group will also set up an R&D center in China to tailor supply requirements for Chinese auto brands.
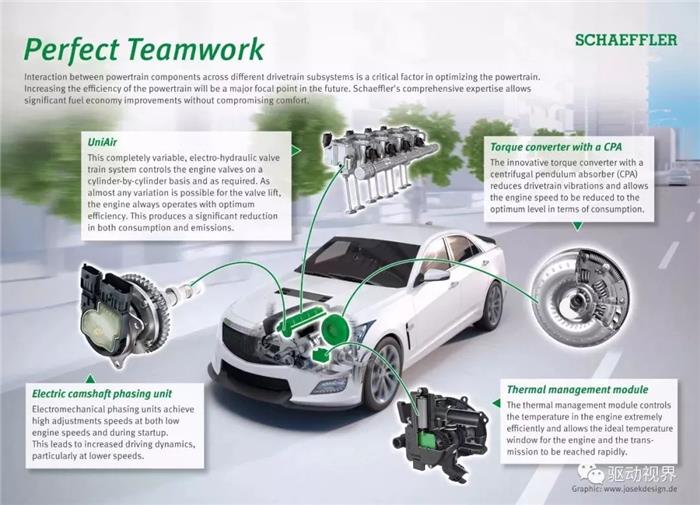

All along, pure electric vehicles are driven by a combination of motor-drive axles. This type of mechanism must add a differential. However, most of this form is not able to keep up with the performance of the motor, and it is necessary to use a speed reducer for deceleration and increase torque. In the role of these institutions, a lot of energy of the motor is used to overcome friction and is not conducive to the use of electric vehicles. But this is also the simplest and most direct form of layout, more like a traditional car.
Schaeffler also has a variety of electric drive solutions. In addition to the P2 hybrid module, Schaeffler also produces electric drive axles. At the same time, it is also developing rim motor technology, but the development of this technology is still in an early stage. According to EV Century, the SV model VV8 of the high-end brand WEY of Great Wall Motor will launch a plug-in hybrid model equipped with an electric drive axle produced by Schaeffler.
Schaeffler hub motors
Future-oriented zero-emissions technologies also have a place in Schaeffler's development concept. The company also demonstrated its hub motor technology at the show, the "E-Wheel Drive" technology, which placed the motor inside the wheel.
In response to the demand for high power and high torque in the European automotive market, Schaeffler Germany has developed a wheeled motor drive system eWheelDrive with an extremely high integration level for Class B and above. The system places the inner rotor motor, power electronics, controllers, brakes, and water-cooling devices in a 16-inch rim.
As a rear-wheel drive, eWheelDrive (β version) is equipped with the Ford Fiesta eWheelDrive electric test vehicle jointly developed with Ford's European Research and Advanced Engineering Center in 2013, capable of providing peak torque of up to 1400Nm, and 88KW of power.
Schaeffler introduced the new technology E-Wheel Drive, which is actually a combination of wheel motors and brakes, and has a great demand for the full range of torque and speed of the motor. The electric vehicle using this technology has higher transmission efficiency, and the braking is achieved by “recovery of kinetic energy†through the motor's reverse hysteresis. The built-in brake drum is used in an emergency and when the battery is full and can no longer accept power. .
Although this form is more energy-efficient, in addition to the cost, the factors that affect the handling of suspension and unsprung masses need to be resolved.
Under the "future mobility" strategic framework, Schaeffler Group will continue to adhere to the research and development of new energy technologies, including wheel hub motor drive systems, to provide more possibilities for future drive. The eWheelDrive in-wheel motor drive technology integrates a separate motor into the two rear hubs of the vehicle, replacing the engine and transmission in conventional transmissions, and the mid-range generator for electric vehicles, saving significant space.
POLYKEN930 is a cold applied tape coating system designed for the corrosion protection of field joints, fittings, and specialty piping. The unique adhesive retains conformability over a wide temperature range, yet exhibits an elevated level of shear resistance, which is a key in-ground performance characteristic. Coupled with a pliable, very malleable polyethylene backing, this versatile tape system can be applied by hand or with a wrapping machine.
Polyken 930 Joint Tape,Pipe Repair Tape,Pipe Joint Tape,Polyken Wrapping Tape,Polyken Joint Wrap Tape,joint wrap tape
Jining Qiangke Pipe Anticorrosion Materials CO.,Ltd , https://www.pipe-wrap-tape.com